11.07.2025
Expanded encoder portfolio
IO-Link interface for easy integration and increased efficiency
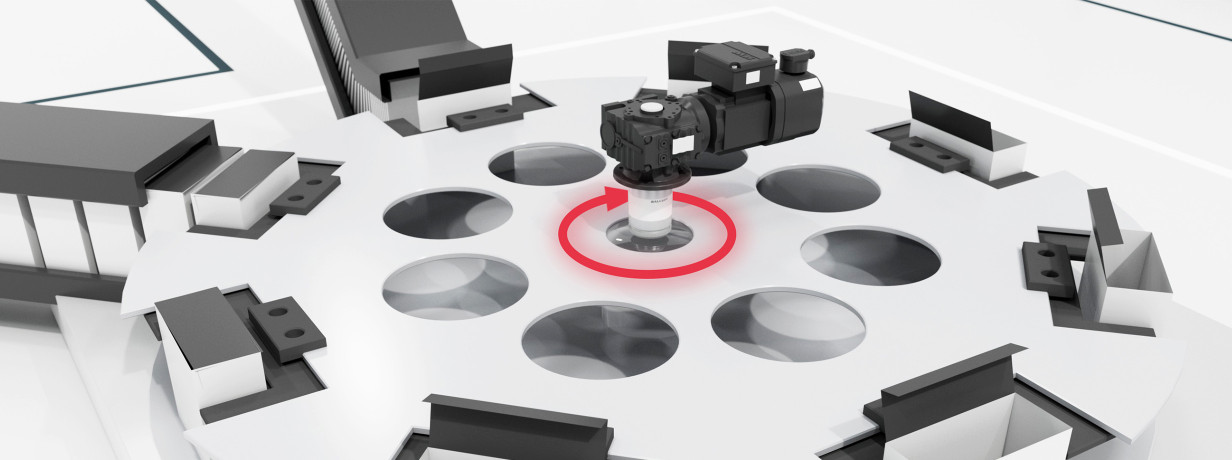
Rotary encoders from Balluff detect absolute rotational positions, speed and rotary movements even under difficult ambient conditions and high shaft loads. Rotary encoders are used wherever movements take place, in automation technology and robotics, or in machine tools and packaging machines.
IO-Link benefits also for rotary applications
We are now expanding our encoder portfolio to include versions with an IO-Link interface, adding rotary applications to the Balluff IO-Link playbook. In addition to Balluff's usual robustness, the rotary encoders also score with particularly easy installation and commissioning and resistance to elevated levels of eletrical noise.
They bring the convincing advantages of IO-Link to typical applications such as grippers, robot arms or the monitoring of roll-to-roll processes with speed and performance that is comparable to standard rotary encoders.
Thanks to its compatibility with any IO-Link master, you also benefit from increased efficiency during integration and the user-friendliness of a single system.
Features
- IO-Link interface (IO-Link COM3)
- Seamless compatibility with the Balluff IO-Link environment
- Improved functionality
- Simplified commissioning
- Robust for industrial applications
- Integrated operating hours counter
- Monitors device temperature and operating voltage
Versatile designs for different applications
Rotary encoder in synchro flange design
For flexible installation in drives and gearboxes
Rotary encoder in clamping flange design
For flexible installation in mechanical engineering
Rotary encoder in hollow shaft version
Ideal for tight installation spaces with perfect axis alignment
Downloads
-
Rotary Encoders: Now With Additional Functions Thanks To Io-Link