05.06.2024
A factory for learning
This is what the Global Production Learning Factory at the production technology laboratory of the Institute of Production Science(wbk) at the Karlsruhe Institute of Technology (KIT) stands for. It is not only a place of learning for students, but also brings science and industry together and is the starting point for innovative cooperation.
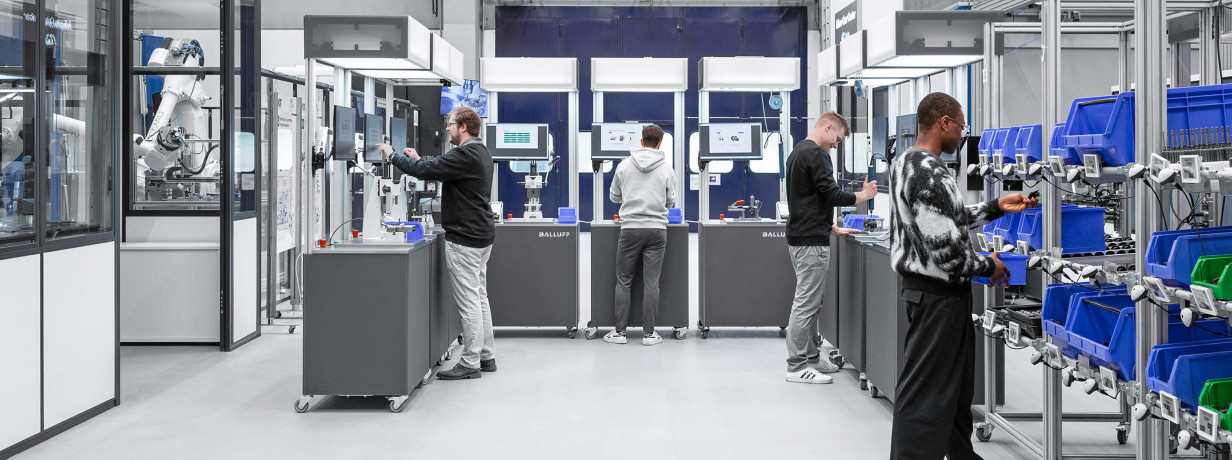
Josip Kopcic knows his way around the Karlsruhe region in southwest Germany. The reason: he has been working in this area as a sales representative in field service for Balluff for almost ten years. He also knows his way around the production engineering laboratory of the Institute of Production Science (wbk) at the Karlsruhe Institute of Technology (KIT). This is where the Learning Factory “Global Production” is located, a demonstration and learning environment for new technologies and processes in production. Kopcic supports the Learning Factory team with his technical know-how, as a member of the jury at the annual hackathon, and by providing automation solutions by Balluff.
The start of an innovative collaboration
The wbk Institute of Production Science has a long history. Founded in 1952 by Professor Dr.-Ing. Walter Schmidt, its development reflects the technological and industrial progress of the past decades. As part of the Karlsruhe Institute of Technology (KIT), it pursues the goal of application-oriented research into new production techniques and the development of new technologies. It is divided into the three main research areas of “Production Systems,” “Machines, Equipment and Process Automation,” and “Manufacturing and Materials Technology.” When Josip Kopcic came by in 2015, bringing along the IO-Link communication standard for a more flexible and efficient production, it marked the start of an innovative collaboration.
At the Learning Factory, students get to experience complex production systems and collect data for their own research.
Linking theory and practice
Gisela Lanza, Director of Production Systems at the wbk, explains the Learning Factory’s basic idea as follows: “Students should have a place where they can put their theoretical questions about the production technology of the future into practice and research them — a ‘factory for learning’, so to speak.” Together with other companies in industry, the wbk and Balluff work to turn these ideas into reality.
“Initially, the Learning Factory was a stationary production system consisting of various stations,” explains Magnus Kandler, who was already on board as a student when the first training courses and workstations were developed and put into operation. Back then, Kandler was working towards a degree in industrial engineering at Karlsruhe and helped set up the Learning Factory. “It is all the more rewarding to continue, develop and shape the project as a research assistant,” says Kandler, whose current work as a Ph.D. student focuses on production system planning and digital shopfloor management.
Applying new production methods
The doors of the Learning Factory “Global Production” are not only open to students. The wbk also offers trainings or lectures for companies and other organizations. “This is an opportunity for us to raise awareness for new manufacturing trends and give companies the chance to experience new technologies and approaches like predictive maintenance, circular economy, or human-robot collaboration for themselves,” says Kandler.
Modular, mobile, and self-sufficient
“For this to be possible, the Learning Factory has to use state-of-the-art technology,” explains Alexander Geiser, who is responsible for the Learning Factory's hardware. “At the institute, we are always looking for ways to use new technologies at the Learning Factory. After all, it is also our flagship not only for teaching and continuing education, but also as a platform for companies to present their innovative solutions.”
During the pandemic, the institute switched to online learning formats. The team used the time to revise the outdated concept. Together with Balluff and other partners, ideas for the further development of the Learning Factory were developed: the goal was to make it modular, mobile, and self-sufficient. In addition, the seamless traceability of individual products using a product passport as well as the topic of the circular economy play an important role.
The workstations consist of the same basic structure. The individual machines required for specific production steps are then mounted on it. The new architecture has significantly reduced the time needed to refit the line.
Today, the Learning Factory consists of ten mobile workstations, each equipped with wireless technology, electronic actuators, and batteries to ensure mobile and self-sufficient operation. All stations have the same design and can be equipped with various tools, machines, or robots based on the requirements of the production process. Two industrial robots, one collaborative robot, and three pneumatic presses complement the ten new stations.
This level of modularity covers a wide variety of industrial scenarios, in order to provide participants with the greatest possible adaptability for their own business purposes. “We focused on a high degree of flexibility, fast retooling, and easy commissioning,” Geiser describes the goal.
The stations‘ design serves as a guide through the production process. The “recipe” for each production step is stored in the system, the part is identified, and displays and light signals indicate what needs to be done in detail. This reduces both the susceptibility to errors and resources needed for training.
Highly appreciated input
Over time, more than 120 individual Balluff components have been installed at the Learning Factory, from IO-Link Wireless masters to RFID read and write heads to detect individual parts to condition monitoring sensors (BCM) which capture environmental data like vibrations, temperature, and ambient humidity alongside process data.
“Initially, we mostly focused on the aspect of traceability and product passports,” says Geiser. “The input we got from Josip Kopcic from Balluff then shifted our focus more to condition monitoring. We highly appreciate the conversation and the impetus.”
“Progress never stops,” Kopcic explains his motivation. “This is why, at Balluff, we’re always trying to find new solutions and to translate trends into practical products. This is also what drives us in regard to the Learning Factory.”
This is also what drives us in regard to the Learning Factory.” The data collected by the BCM, for example, can be used to detect anomalies during the production process and draw conclusions about the condition of the system. This results in many approaches for developing new solutions in the field of predictive maintenance using i.e. artificial intelligence and machine learning. An ideal basis for students to test the various approaches.
Pulling all-nighters for the best idea
Balluff’s involvement is not, however, limited to hardware. The sensor and automation specialist also supports the annual hackathon. Around 30 students spend 30 hours at the Learning Factory working on several cases. The resulting ideas are presented and evaluated by a jury of experts from industry and science based on various criteria such as effectiveness, originality, and maturity or the underlying business model and market potential.
The winning team receives a handsome prize of more than $1,600. “Everyone gives it their best at the hackathon. You can feel the motivation and passion in the room. It is fascinating to see how the teams develop new solutions in such a short time,” says Kopcic, who is also a member of the jury.
Magnus Kandler (left) and Alexander Geiser (right) are academic staff and doctoral candidates at the wbk. Mr. Kandler is part of the Production System Planning group and researches digital shopfloor management. He holds training courses for companies in the Learning Factory and is responsible for business models. Alexander Geiser works in the quality assurance group and is involved in the remanufacturing of fuel cell components in the context of e-mobility.
Win-Win situation
“The research at the Learning Factory as well as the training sessions and the hackathon are our flagship,” says Kandler. “When you enter our facilities, the mobile workstations are one of the first things you see. This also serves as a conversation starter with partners, students, and companies.” For Balluff and the wbk, the involvement creates a win-win situation: “The students come into contact with our solutions. Many of them start their own businesses after they graduate or find a job in industry. A few of them remember us, which has already resulted in numerous projects,” Kopcic says happily.